In every industry, the significance of top quality tools can not be overemphasized. From building and construction and automobile to woodworking and engineering, tools are the backbone of effective and accurate work. However have you ever questioned the intricate process behind tool production? In this short article, we will delve into the art and science of tool production, checking out the meticulous workmanship and advanced innovations that go into producing tools renowned for their accuracy, durability, and reliability.
Style and Engineering:
The journey of tool manufacturing starts with style and engineering. Competent designers and engineers work together to produce blueprints and 3D models that record the wanted requirements and functionalities of the tool. They consider elements such as ergonomics, product choice, and efficiency requirements to make sure optimal functionality and user experience.
Product Selection:
Selecting the ideal products is essential in tool manufacturing. Tools are normally made from premium alloys and steels that use a balance of strength, resilience, and resistance to use and corrosion. Each tool type needs specific product residential or commercial properties to endure the forces and stresses come across throughout use. For example, drill bits need tough and heat-resistant products, while wrenches demand high tensile strength.
Accuracy Machining:
Precision machining is a basic process in tool manufacturing. Advanced machining methods, such as computer mathematical control (CNC) machining, are employed to form and form the tool components with exceptional accuracy and consistency. CNC machines make use of computer-controlled movements to specifically cut, drill, and mill the raw products, transforming them into detailed tool parts.
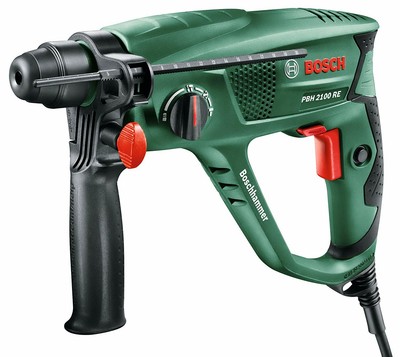
Heat Treatment:
Heat treatment is a critical step that improves the strength and solidity of tool parts. Through procedures like tempering, satiating, and annealing, the products undergo regulated heating and cooling cycles. This alters the microstructure of the products, resulting in improved durability, solidity, and resistance to contortion or damage. Heat treatment ensures that the tools can withstand demanding applications without compromising their performance.
Covering and Finishing:
To even more enhance the sturdiness and performance of tools, various coatings and surfaces are applied. For instance:
a. Difficult finishings: Tools like drill bits and milling cutters frequently get tough coatings, such as titanium nitride (TiN) or titanium aluminum nitride (TiAlN). These finishings provide increased wear resistance, lowered friction, and extended tool life.
b. Anti-corrosion coatings: Tools used in damp or destructive environments, such as wrenches or pliers, are typically treated with anti-corrosion finishes. These finishings avoid rust development and make sure long-lasting performance.
c. Polishing and grinding: Tool surfaces are carefully polished and ground to eliminate any flaws or rough edges, ensuring smooth operation and lessening the danger of damage to workpieces.
Quality Control:
Strict quality control procedures are implemented throughout the production procedure to guarantee that the tools satisfy the highest requirements. Tools go through thorough assessments, consisting of dimensional checks, hardness testing, and practical evaluations. Advanced technologies, such as coordinate determining machines (CMMs) and non-destructive testing approaches, are used to make sure the tools' accuracy, dependability, and adherence to requirements.
Continuous Development:
Tool manufacturers are constantly striving for development, seeking ways to improve tool performance, sturdiness, and user experience. They purchase research study and advancement to include new products, style enhancements, and production methods. Continuous improvement makes sure that tools develop to fulfill the ever-changing needs of markets and users.
Conclusion:
Tool manufacturing is a precise blend of craftsmanship and advanced technology. From the preliminary style and engineering stages to the accuracy machining, heat treatment, covering, and quality assurance procedures, every step is taken with precision and care. The result is a vast array of high-quality tools that empower professionals and lovers to accomplish amazing resultsin their particular fields. The art and science of tool manufacturing guarantee that these necessary instruments embody precision, durability, and reliability. It might sound far-fetched, but it's all true! Why don't you check
chipping hammers out at https://www.vingle.net/posts/6111884 and see what you think!
As you reach for your dependable tools throughout your next project, take a minute to value the workmanship and know-how that went into their development. The meticulous style, product choice, precision machining, heat treatment, covering, and quality control processes all contribute to the tools' performance and longevity. By integrating conventional workmanship with advanced technologies, tool manufacturers continue to press the borders of development, offering tools that meet the ever-growing needs of markets and users. So, the next time you hold a well-crafted tool in your hand, remember the complex journey it undertook-- from idea to development. It is a testament to the dedication and passion of the tool production market, allowing you to tackle your tasks with confidence and attain exceptional outcomes.
Learn more:
https://dictionary.cambridge.org/us/dictionary/english/chisel